The goal of every producer is to deliver high-quality products and increase customer satisfaction continuously. A proven way to achieve this is via process optimization driven by IoT and AI-based solutions, however, only about 12% of manufacturers have leveraged these technologies successfully.
Several surveys have revealed that, while most manufacturers want to adopt these technologies, there are often questions around the cost and complexity of the solutions, their potential value and if it will really affect their bottom line and yield desired results.
In this article, we’ll look at why IoT and AI are redefining the manufacturing industry, what purpose they serve, and how enterprises can leverage them.
Table of Contents
Production Efficiency
Managing and optimizing process parameters to predict current production quality and identifying correlations between input parameters and outcomes.
A system that combines the power of Industrial IoT and AI, can run simulations and analyze current and future alternatives to provide real-time recommendations for the most viable and optimal manufacturing process that ensures wasteful outcomes are minimized.
These systems give a manufacturer insights into the factors, some of which may have been trivialized, that play crucial roles in product quality outcomes and help forecast expected quality outcomes based on current conditions.
According to a survey conducted by the American Society for Quality(ASQ), manufacturing companies that have digitized their operations and leverage IoT in multiple ways have achieved up to an 82% increase in production efficiency and 49% fewer product defects.
A good example of one such company is power tools manufacturer, Stanley Black & Decker, which integrated IoT into their production process to reduce down time, and improve the quality of outputs.
The approaches adopted by Stanley Black & Decker is proof that Industrial IoT solutions don’t need to be complex to be effective. For example, to reduce production downtime, one of the approaches adopted involved the use of RFID tags on finished products, with an RFID scanner located at the end of each production line. The Scanner counts the number of products being shipped off that line in real-time, and immediately the number starts falling below expected values, the factory managers and technicians are alerted. With this, they are able to quickly determine the cause of reduction in output which ranged from employee fatigue to machines gradually failing.
While the solution is still being rolled out across their factories worldwide, factories, where IoT solutions for improved operational efficiency were deployed, have already been experiencing a 10% greater reduction in downtime, and output quality improvement with over 16.5% reduction in scrapped products.
Predictive Maintenance (PdM)
Predicting when and how a part or whole of a system or machine may fail before it eventually does.
Preventive maintenance is planned maintenance; it is maximizing the life and uptime of your machine.
Real-time data from multiple IoT enabled sensors, inbuilt or attached to factory equipment and machines, ensures; faults, wears. Tears etc, which may not be immediately obvious to the human eye, are detected.
By feeding this data into AI and Data analysis systems, factory operators can predict equipment or machine’s potential failure and be proactive by immediately scheduling maintenance, rather than the usual reactive measures that lead to longer downtime due to delays in parts supply and other maintenance bottlenecks.
A study by Wall Street Journal found that 42% of industrial manufacturers face unplanned downtime due to equipment failures. These downtimes, when not quickly addressed, usually lead to the factory losing millions either in raw materials going to waste or in unproduced goods depending on the industry. With IoT however, these risks can be mitigated.
PdM is one of the most popular applications of IoT in industrial settings, and use cases abound. An example of a company using IoT and Data Analytics/AI for their PdM efforts is Nissan.
Nissan uses the PdM platform, Senseye, to remotely monitor over 30 different machines including robots, conveyors, drop lifters, pumps, motors and press/stamping machines across multiple global factories where different car models like the Infiniti and X-trail are produced.
Real time data from the machines are fed into Senseye’s proprietary AI software, which helps predict potential failures, provides real-time insight on the health of the machines, and gives 2-14 weeks advance warning of asset failure. All of these have so far helped Nissan to save multi-million dollars which would have been lost to unplanned downtimes.
Quality control with IoT and AI
Detecting and monitoring through vision intelligence.
Being able to perform high-quality inspections at every stage of your production is vital for business success. Reliance on manual quality control has high rates of scrap and defect rejects due to several factors chief of which is human error. Using IoT, detection of defects is much quicker and, thus, ultimately, saves the business money.
In the age of Industry 4.0 a lot of applications like inspecting products with the human eye etc, have been replaced with computer vision based systems which allows manufacturers spot errors and real-time defects in their products or processes. Combined with AI and data analytics, systems can be trained to auto detect defective products and automatically remove the production line. In applications that are too extreme for humans, like heat furnaces, the use of IoT has even further reduced the amount of trial and error as the system is able to determine when the product is ready and when it is not, removing the challenges with uneven quality across production output.
Aside from vision-based applications, Traditional sensors like an end-of-line sensor can be equipped with IoT capabilities to aid and automate the process of tracking defects. So, something like a microscopic crack in your equipment or an inconsistent movement of your machine will not go unnoticed by the system.
Poland Based Furniture Giant IKEA, manufactures furniture boards that are automatically film-laminated. As part of product’s quality requirements, it was important to ensure the quality of the film-lamination meets specified standards. However, due to the potentially hazardous nature of the machine (speed of its conveyor, up to 52 m/min) and other factors like possible human error, it was critical to find a solution that can do this autonomously, safely and accurately. To achieve this, IKEA adopted a bespoke solution based on Cognex’s In-sight vision system, and they were able to achieve a reduction in production waste and guarantee that products fully satisfy quality requirements.
IoT and AI for Health and Safety
An important factor of production is the human workforce and while things like increasing efficiency and productivity are usually viewed as a great way to cut cost, improving safety too can reduce cost, by ensuring employees are protected from fatal and non-fatal accidents, and its related costs, from settlements, legal fees and bad press, to hiring and training replacements.
To put a potential number to it, according to an HSE report in 2017, there were about 159 court cases related to accidents in the manufacturing sector and the average fine per case was around $213,271, not excluding legal fees.
According to data from NSC(the US National Safety Council) the three prominent causes (jointly accounts for over 84% of accidents) of work related injuries are; Contact with Objects and equipment, overexertion, and the tripartite action of slips, trips and falls.
All of this however, are things that could be monitored with a combination of IoT and AI. To mention a few scenarios;
- Personnels can be accessed using computer vision systems placed at the entrance to the factory floor to ensure they are putting on adequate protective gear.
- Smart cameras installed across the factory could examine employees posture, face and general cadence and compare it with their previous behaviors to determine if they need to take a break.
- Sensors on equipment can detect when moving parts are opened or when operators are not properly dressed and turn off the equipment.
- Oil and water spills on the factory floors can be detected using AI powered vision systems and immediately alert floor cleaners.
- Use of Wearables like smart jackets which monitors different safety parameters and reports to a company cloud/edge based monitoring station.
Source: Eleksen
The possibilities are endless.
Several manufacturing companies are already adopting IoT and AI to ensure Employee safety on the factory floor. One of such companies is Daikin Industries, a fluorine-based chemicals manufacturer with 2 plants in Japan. Dalkin wanted a solution to keep its employees safe, enforce compliance to safety measures, and ensure quick response in case of emergency. To achieve this, they adopted a Wearable armband developed by Fujitsu. The armband features sensors to detect fall and recovery, location, proximity to dangerous chemicals and other factors that could affect safety. Data from the sensors are sent to a dashboard and connected to an alarm to ensure that in the event of an accident, the employee can be quickly located and attended to.
IoT and AI: Robotic Collaboration
Robots and humans working together to increase production.
There’s a limit to the number of hours that humans can work. But for robots, this is obviously not the case. However, safety conditions have prevented the usage of robots to their full potential, as they are only restricted to a certain area and certain types of tasks, due to the fear of accidents arising from their collision with humans working on the factory floor.
Leveraging IoT and AI powered positioning and navigation systems, companies like Veo Robotics are gradually solving this problem. Robots can work side by side with humans, doing the heavy liftings and strenuous work, while humans come in with precision and experience. These will reduce employee fatigue and increase productivity.
Increased Revenue
Making optimal use of available resources for maximum results or reducing cost by identifying inefficiencies
Cost optimization is one of the major benefits of leveraging AI and IoT based systems in production. All previously mentioned points lead here.
AIot systems enable boost revenue directly and indirectly in a number of ways including but not limited to;
1. Predictive maintenance features offered by AIoT based systems ensures revenue lost to unscheduled down-times is reduced enabling production to run without hindrances and increasing production efficiency.
2. Equipment monitoring ensures the state of every part of the machine is known, and faults can be easily diagnosed and rectified when they occur. Reducing revenue lost due to time-wasting.
3. Remote monitoring and equipment operations enable employees to perform their duties more effectively, improving their efficiency and contributions.
4. Sensors can keep track of the manufacturing process to solve and prevent bottlenecks, thereby increasing efficiency and gaining maximum ROI.
5. Human errors in quality control are eliminated by using smart systems. This will generally improve the quality of the company’s product, which will in turn increase adoption and boost customer loyalty and ensure increased revenue via increased sales.
6. Employee safety. By implementing AI and IoT systems that detect safety violations, employee safety can be guaranteed and the disruption it causes for the company and production can be averted.
IoT reduces costs by prioritizing and reducing the impact of productivity congestion by offering process optimization and analysis and conditional analysis to make sure humans and machines are working in perfect harmony.
Companies that don’t use IoT for cost optimization could be spending more money than they need to. According to McKinsey & Co this amounts to about $11.1 trillion being wasted currently.
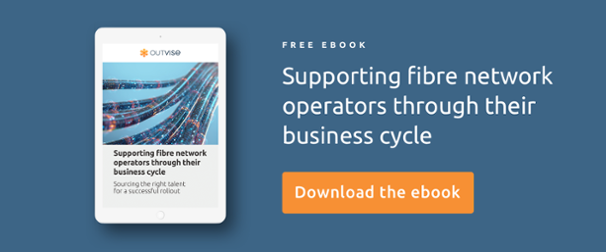
To conclude…
While using IoT and AI could be key to maximizing profits and improving service delivery and product quality for most companies, achieving it has been difficult for many. This may be because businesses believe that the transformation process is complex and costly, but some of the use cases discussed above have shown that this may not always be the case. In most successful deployments, one thing that has proved a decisive factor, is working with experts who share your budget concerns, understand that no two use cases or applications are the same, and are at the same time, patient and skilled enough to identify and understand the peculiarity of your project. That’s where the Outvise talent marketplace can help. The pool of professional experts will help to transform your organization into a results-driven company that saves time for you and your team.
Hardware Design Engineer, IoT Solutions Architect, and Entrepreneur. Emmanuel is currently an ML/IoT hardware Design/ Architecture Specialist at VisionX; working in the Sight team, developing computer vision solutions being used by several fortune 500 companies.
No comments yet
There are no comments on this post yet.